Removing rust from water jacket
Moderators: John@sos, charlesp, Charles uk, RickUK, Petergalileo
Re: Removing rust from water jacket
Has anyone tried Molasses I had some success with it a couple years ago though I haven't used it on a
Seagull barrel yet going to make a new mix this week.
Found this on the Old Marine Engine site anyone tried this-
RUST REMOVAL
Rust can be safely removed off of STEEL parts by converting the rust itself, i.e. FeO2 and Fe2O3. Rust, hydrated iron, can be chemically "reduced", that means converted from a bonded molecule to a simple molecular Fe with free disassociated floating anions, by attacking the rust molecule with a charged molecule of something that likes bonding better than Fe. For this case Zinc works great.
How is this done, chemical reactions of this nature generally work faster with higher temperatures, a fluid bath is needed to better transport the replacement molecule to target areas. The Zinc must be turned into molecular Zinc and electrically charged to go after the rust and replace the Fe molecule with itself.
Now that is the theory so how do we get there?? Iron is pretty much impervious to alkaline solutions but dissolves in most acids. Zinc will dissolve in just about anything. We make up a solution of lye ( Caustic soda) and water at the ratio such that the water will boil at approximately 132 Deg c, well above the normal 100 Deg C. (50/ 50)Toss in some Zinc, preferably Zinc Oxide or just dirty Zinc. The Zn dissolves into the NaOh (lye) and leaves the Zn now charged positive. Since Zinc likes to bond to things better than Iron (Fe) the Zn+ molecule attacks the rust and takes the Iron molecule off and bonds itself to the Oxygen molecules that made up the rust. BUT in doing so it winds up floating in the solution. The result, the rust gets stripped off the Iron part, the Iron itself is untouched. This type of process has absolutely no bad effects to the original part just to the rust on the part. If you were to try an acid dip it would attack the base metal itself, the iron part.
The next trick in using this is as follows;
Hang the part on a piece of steel wire in the solution so you can pull it out from time to time and check it. I use safety wire for bolt heads. When the parts are done rinse them under lots of COLD running water. Next I immediately drop the parts into a solution of oily gasoline or thoroughly spray down with WD-40 to displace any water on the surface, sometimes then heat the part on a tin can lid (lid from the coffee can) to warm the part and drive off any remaining water in the pours of the metal, helps drive the oil into the surface as a preservative effect.
Cool trick of this process is that the lye being alkaline it treats the micro surface of the part and inhibits rust formation on a raw metal surface. If you try to acid dip a part it will always leave micro deposits of acid in the pours of the metal and it will re-rust in a matter of days. In an alkaline process this will never happen. If you see a gray smut form on the surface that is the carbon found in steel, part of the manufacturing process to make steel out of iron. Carbon is inert to these solutions so when the rust is dissolved into the solution it leaves behind the contained carbon. Just wash if off, I often use a tooth brush.
John
Seagull barrel yet going to make a new mix this week.
Found this on the Old Marine Engine site anyone tried this-
RUST REMOVAL
Rust can be safely removed off of STEEL parts by converting the rust itself, i.e. FeO2 and Fe2O3. Rust, hydrated iron, can be chemically "reduced", that means converted from a bonded molecule to a simple molecular Fe with free disassociated floating anions, by attacking the rust molecule with a charged molecule of something that likes bonding better than Fe. For this case Zinc works great.
How is this done, chemical reactions of this nature generally work faster with higher temperatures, a fluid bath is needed to better transport the replacement molecule to target areas. The Zinc must be turned into molecular Zinc and electrically charged to go after the rust and replace the Fe molecule with itself.
Now that is the theory so how do we get there?? Iron is pretty much impervious to alkaline solutions but dissolves in most acids. Zinc will dissolve in just about anything. We make up a solution of lye ( Caustic soda) and water at the ratio such that the water will boil at approximately 132 Deg c, well above the normal 100 Deg C. (50/ 50)Toss in some Zinc, preferably Zinc Oxide or just dirty Zinc. The Zn dissolves into the NaOh (lye) and leaves the Zn now charged positive. Since Zinc likes to bond to things better than Iron (Fe) the Zn+ molecule attacks the rust and takes the Iron molecule off and bonds itself to the Oxygen molecules that made up the rust. BUT in doing so it winds up floating in the solution. The result, the rust gets stripped off the Iron part, the Iron itself is untouched. This type of process has absolutely no bad effects to the original part just to the rust on the part. If you were to try an acid dip it would attack the base metal itself, the iron part.
The next trick in using this is as follows;
Hang the part on a piece of steel wire in the solution so you can pull it out from time to time and check it. I use safety wire for bolt heads. When the parts are done rinse them under lots of COLD running water. Next I immediately drop the parts into a solution of oily gasoline or thoroughly spray down with WD-40 to displace any water on the surface, sometimes then heat the part on a tin can lid (lid from the coffee can) to warm the part and drive off any remaining water in the pours of the metal, helps drive the oil into the surface as a preservative effect.
Cool trick of this process is that the lye being alkaline it treats the micro surface of the part and inhibits rust formation on a raw metal surface. If you try to acid dip a part it will always leave micro deposits of acid in the pours of the metal and it will re-rust in a matter of days. In an alkaline process this will never happen. If you see a gray smut form on the surface that is the carbon found in steel, part of the manufacturing process to make steel out of iron. Carbon is inert to these solutions so when the rust is dissolved into the solution it leaves behind the contained carbon. Just wash if off, I often use a tooth brush.
John
- Rob Ripley
- Posts: 442
- Joined: Fri Mar 10, 2006 11:38 am
- Location: Melbourne, Australia
Re: Removing rust from water jacket
That sounds good John, how can you tell if it has reached and/or is effective on the internal section of the barrel - the part that is not visible ?
Re: Removing rust from water jacket
The only way to check blind areas would be to a drill hole then plug it (Dont ask me where to drill).
Using Molasses is very slow also it stinks last time I used molasses it took a week to clean some cast
brackets. With a barrel I will take it out a couple times a week and give it a high pressure clean then
replace it in the Molasses could take up to a month. When I do it I will take before and after photo's.
, have a look at this you tube clip.
http://www.youtube.com/watch?v=8-gBAjEg ... el&list=UL
Heres a couple of replies on the Old Marine Engine site (Rust Removal with Zinc) I have not tried this.
Mate this process works like nothing i have ever seen, removes everything, and im not joking, my super pup came up better than i expected inside and out, takes a bit of time and zinc but its worth it, when the process starts to slow down, you change the lye and zinc and off she goes again, it can get very reactive, so watch out, cool. i have a cut off 44 gallon drum that i use, go down to the local slip way and scab up some zinc, easy peazy, Cheers
This method is perfect for the water channels, I removed the welsh plugs and filled the water channels with small pieces of zinc, Its very surprising the amount of rust that is removed, I could not fit the blade of a screwdriver into the gap in the water jacket, now it about 1/2 an inch. clean as a whistle, i have also filled the back of my new brass welsh plugs with zinc to stop further corrosion in its new life.
John
Using Molasses is very slow also it stinks last time I used molasses it took a week to clean some cast
brackets. With a barrel I will take it out a couple times a week and give it a high pressure clean then
replace it in the Molasses could take up to a month. When I do it I will take before and after photo's.
, have a look at this you tube clip.
http://www.youtube.com/watch?v=8-gBAjEg ... el&list=UL
Heres a couple of replies on the Old Marine Engine site (Rust Removal with Zinc) I have not tried this.
Mate this process works like nothing i have ever seen, removes everything, and im not joking, my super pup came up better than i expected inside and out, takes a bit of time and zinc but its worth it, when the process starts to slow down, you change the lye and zinc and off she goes again, it can get very reactive, so watch out, cool. i have a cut off 44 gallon drum that i use, go down to the local slip way and scab up some zinc, easy peazy, Cheers
This method is perfect for the water channels, I removed the welsh plugs and filled the water channels with small pieces of zinc, Its very surprising the amount of rust that is removed, I could not fit the blade of a screwdriver into the gap in the water jacket, now it about 1/2 an inch. clean as a whistle, i have also filled the back of my new brass welsh plugs with zinc to stop further corrosion in its new life.
John
Re: Removing rust from water jacket
I had forgotten about molasses. Have some surface rust inside a steel SD tank. This might be the answer. Wonder what ratio I should use?
- Stelios_Rjk
- Posts: 1458
- Joined: Sun Jun 17, 2012 10:15 pm
- Location: Athens - Greece
Re: Removing rust from water jacket
Impresive infos!! Thank you very much! One derusting agent I used (evaporust) must be based on molasses, the maker says that is his staff is biodegradable, non toxic and no corrosive. About mixture I read in Wikipedia that it is 1 part of molasses to 10 parts of water.
I read about the method with the zinc. I think it is the best. It is not like electrolysis which is a "line of sight" method. Wherever the solution goes, rust is removed. In general terms this method goes like this. In a solution with NaOH you add zinc. Zinc is dissolved. You add the rust part. Rust is ferric oxide, which means ferrum and oxygen. Due to electrochemical series of metals the zinc "steals" the oxygen from the rust, so rust is converted to ferrum. This method works for the same reason that galvanic corrosion works. Pretty cool!
I read about the method with the zinc. I think it is the best. It is not like electrolysis which is a "line of sight" method. Wherever the solution goes, rust is removed. In general terms this method goes like this. In a solution with NaOH you add zinc. Zinc is dissolved. You add the rust part. Rust is ferric oxide, which means ferrum and oxygen. Due to electrochemical series of metals the zinc "steals" the oxygen from the rust, so rust is converted to ferrum. This method works for the same reason that galvanic corrosion works. Pretty cool!
I love the 10600/145 turns!!!
- Charles uk
- Posts: 4972
- Joined: Wed Feb 27, 2008 4:38 pm
- Location: Maidenhead Berks UK
Re: Removing rust from water jacket
Can someone do a clinical trial, on this method with a cracked block?
heat dry & weigh to 1 gram
photographs
weight after treatment
condition of bore afterwards
pics of sections of block to see how far it penetrated into the shadowed areas.
We can't endorse a method of derusting until we're certain it will do the the job without causing more problems than it cures!
heat dry & weigh to 1 gram
photographs
weight after treatment
condition of bore afterwards
pics of sections of block to see how far it penetrated into the shadowed areas.
We can't endorse a method of derusting until we're certain it will do the the job without causing more problems than it cures!
Make it idiot proof and someone will make a better idiot.
Re: Removing rust from water jacket
..and, I suggest, a 'before and after' set of photos of the cylinder head and gasket.
- Stelios_Rjk
- Posts: 1458
- Joined: Sun Jun 17, 2012 10:15 pm
- Location: Athens - Greece
Re: Removing rust from water jacket
At this times and for a couple of days I am curring one block with electrolytic derusting. In the evening I will post pictures. As far as I can see there is some results but not something impressive, seems to work but doesn't clear the waterways. I am tempted to try the method with the zinc but I don't have a way to measure with one gram precision the weight.
I love the 10600/145 turns!!!
- Rob Ripley
- Posts: 442
- Joined: Fri Mar 10, 2006 11:38 am
- Location: Melbourne, Australia
Re: Removing rust from water jacket
Regardless of the method,I can't see how you can tell if it works in the areas that are not visible and/or accessable with a scraper -- I keep getting back to the only way to be sure is to bore an inspection hole and plug it, like the welsh plug on a car block.
Re: Removing rust from water jacket
A flexible borescope would enable you to see inside the block if you can find an engineering company that has one.
Re: Removing rust from water jacket
All
Suggest this simple technique to check the hidden gallery behind the exhaust port.
1. Take a piece of wire diameter 1.6mm
2. Bend the last inch to 90 deg
3. thread it thru the water jacket & into the hidden gallery
4. simultaneously repeat with an identical wire from the opposite side
This process will allow you to gauge the cross section of the hidden gallery
You'd need a very good bore-scope to inspect. Mine is dia 12mm. Better ones are dia 9mm. Difficult to go around a corner.
RexNZ
Suggest this simple technique to check the hidden gallery behind the exhaust port.
1. Take a piece of wire diameter 1.6mm
2. Bend the last inch to 90 deg
3. thread it thru the water jacket & into the hidden gallery
4. simultaneously repeat with an identical wire from the opposite side
This process will allow you to gauge the cross section of the hidden gallery
You'd need a very good bore-scope to inspect. Mine is dia 12mm. Better ones are dia 9mm. Difficult to go around a corner.
RexNZ
- Charles uk
- Posts: 4972
- Joined: Wed Feb 27, 2008 4:38 pm
- Location: Maidenhead Berks UK
Re: Removing rust from water jacket
Very late model Centurys were fitted with a water feed into the exhaust, there are several posts on the subject on here, perhaps the inspection hole that Rob suggests could be utilised for this purpose.
Maybe this was ones of the reasons that Seagull started to allow some of the cooling water into the exhaust from there,
Quieter exhaust note,
Cooler exhaust gas,
No trapped water pocket.
Seek & ye shall find!
Maybe this was ones of the reasons that Seagull started to allow some of the cooling water into the exhaust from there,
Quieter exhaust note,
Cooler exhaust gas,
No trapped water pocket.
Seek & ye shall find!
Make it idiot proof and someone will make a better idiot.
- Stelios_Rjk
- Posts: 1458
- Joined: Sun Jun 17, 2012 10:15 pm
- Location: Athens - Greece
Re: Removing rust from water jacket
Here comes the pictures. This is before.
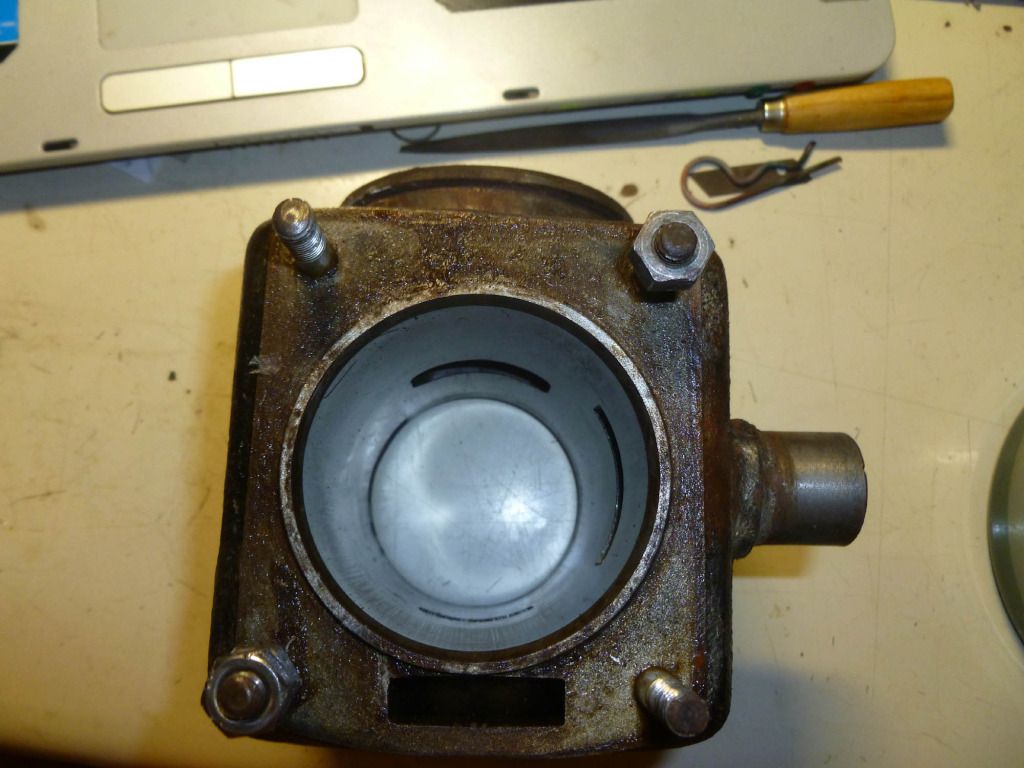
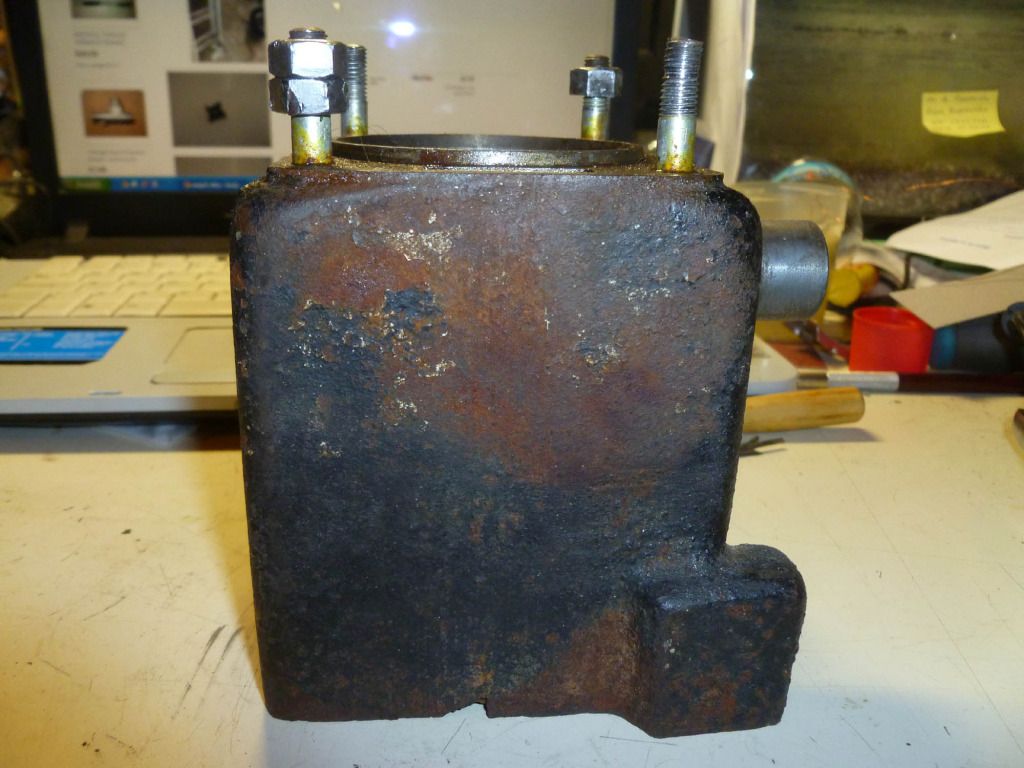
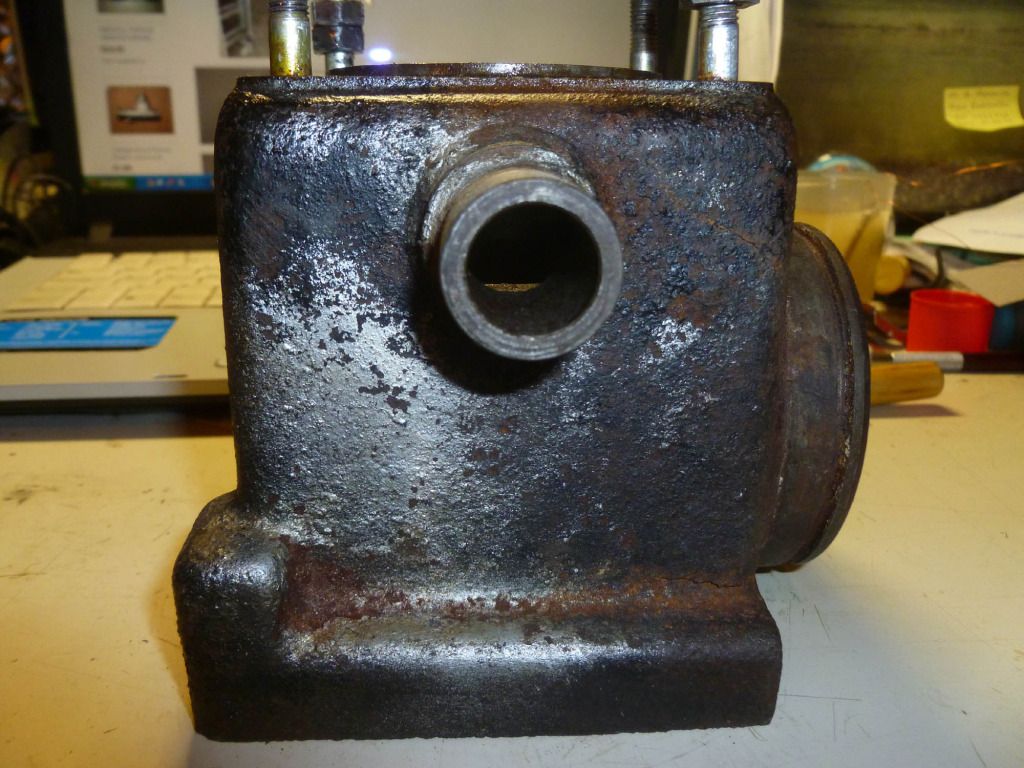
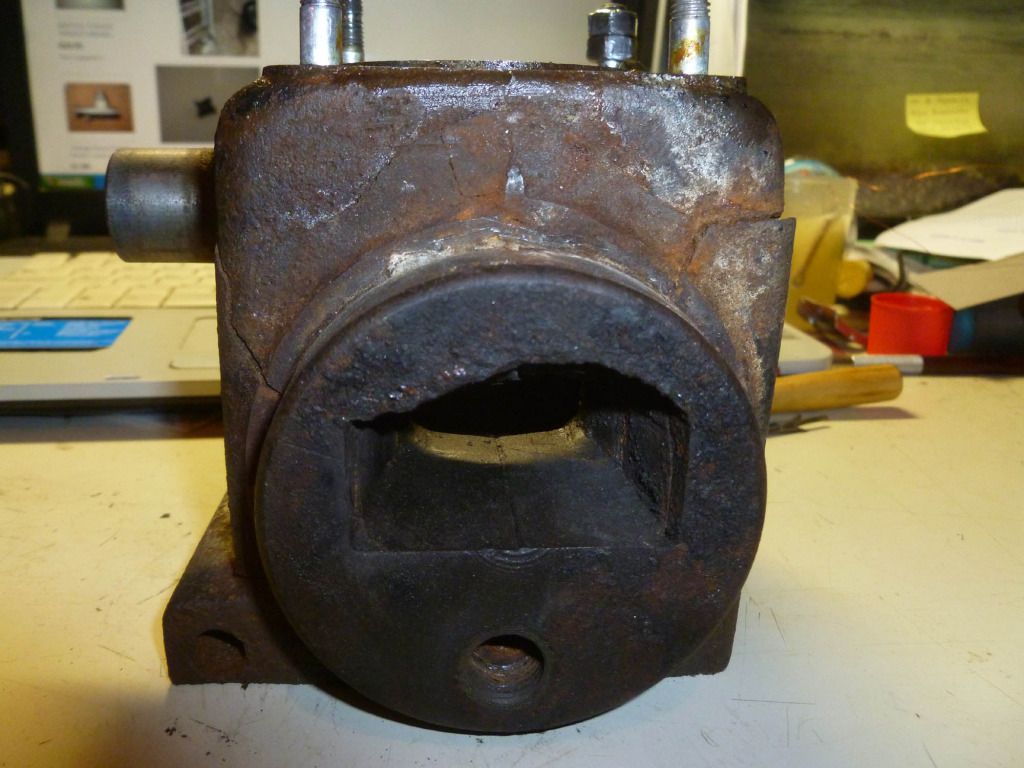
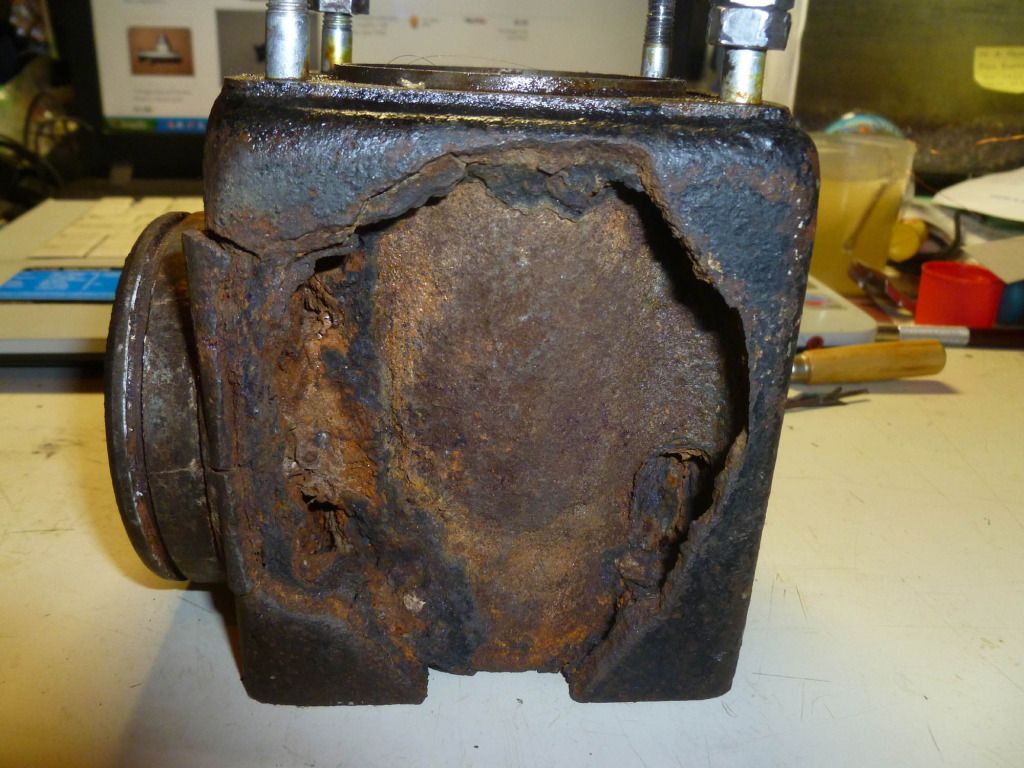
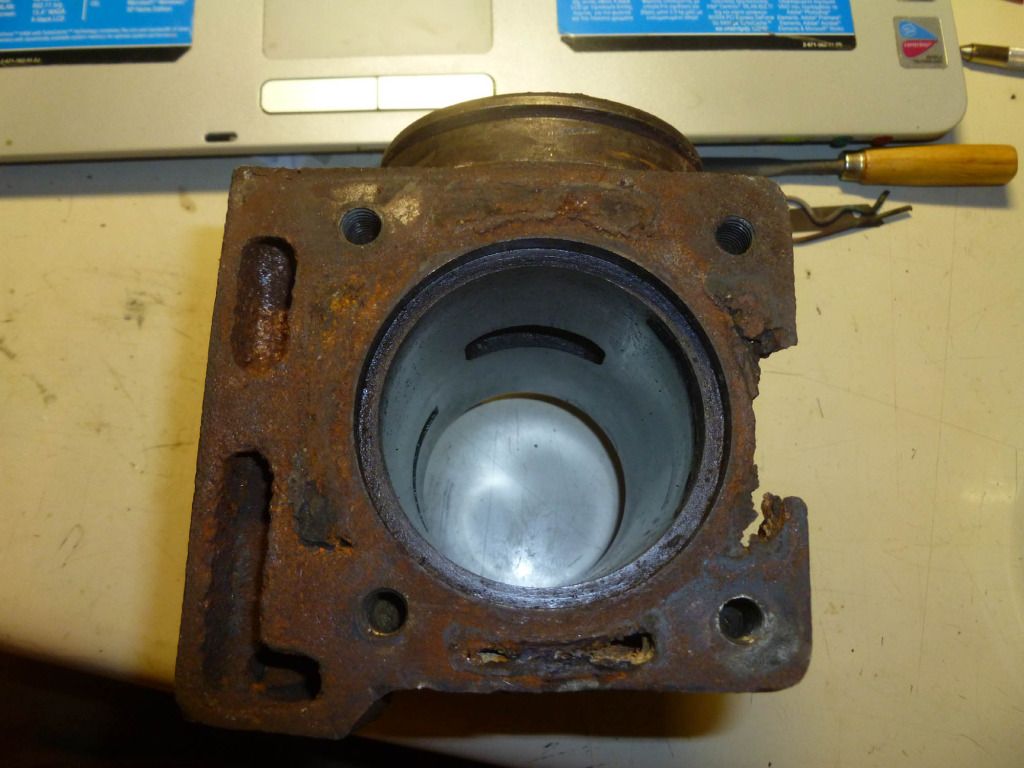
And this is after.
This is rust floating. I have changed the solution 3-4 times removing such amounts of rust but according to the visible results the procedure has to continue for many more days.
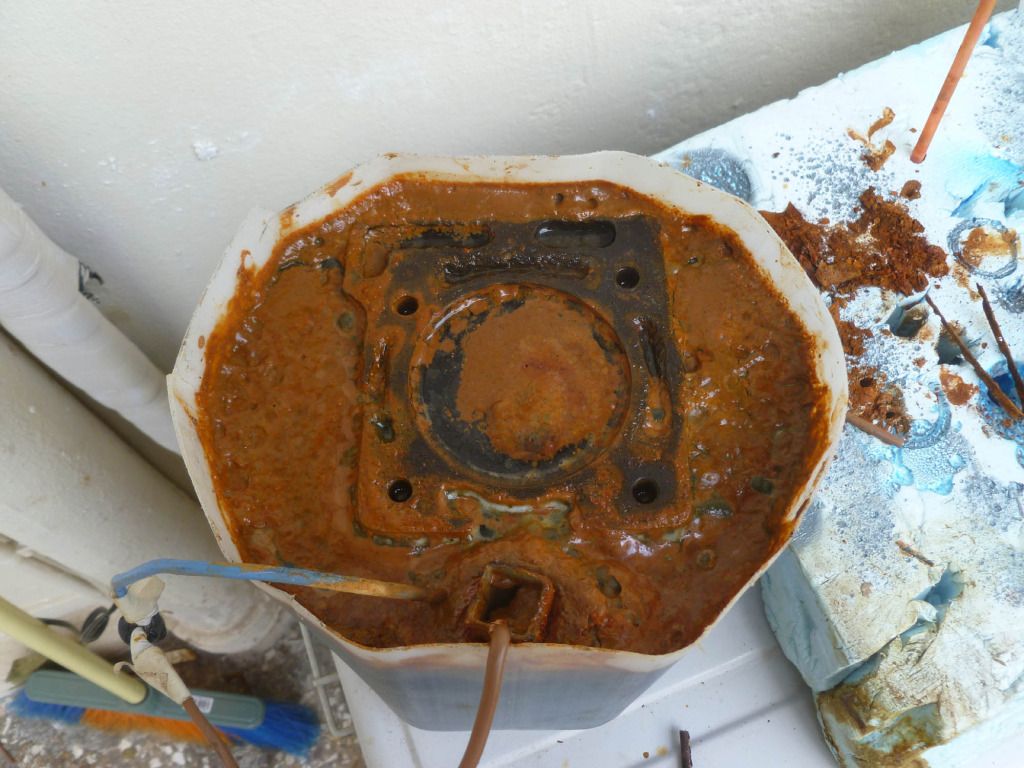
One sacrificial electrode.
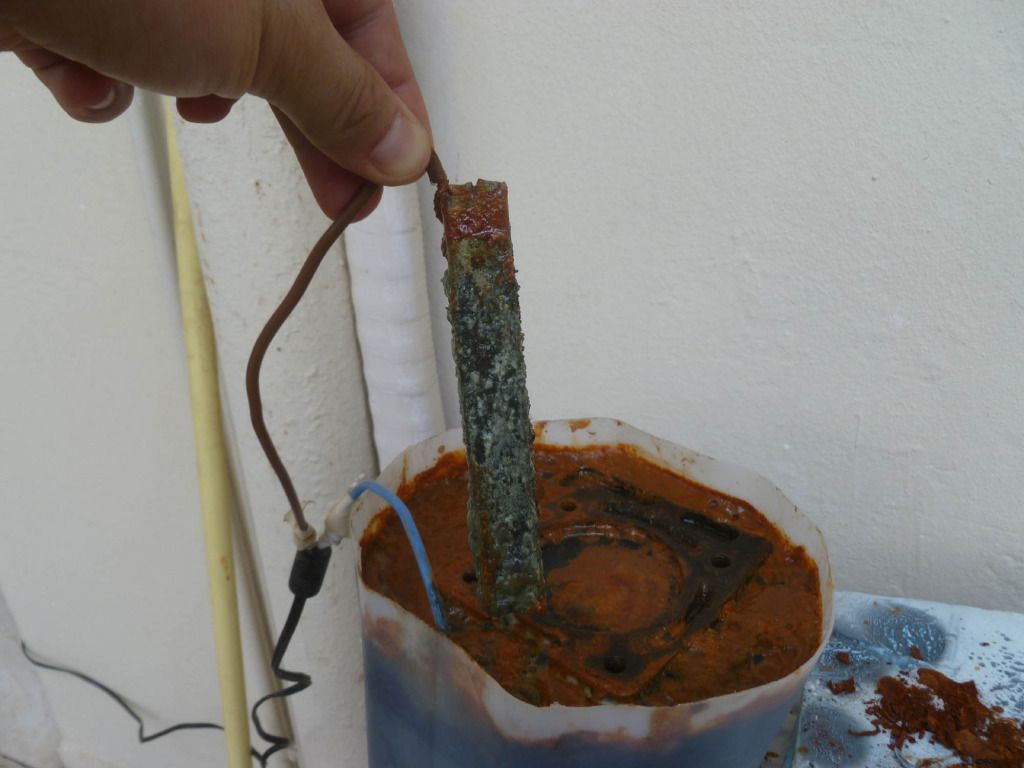
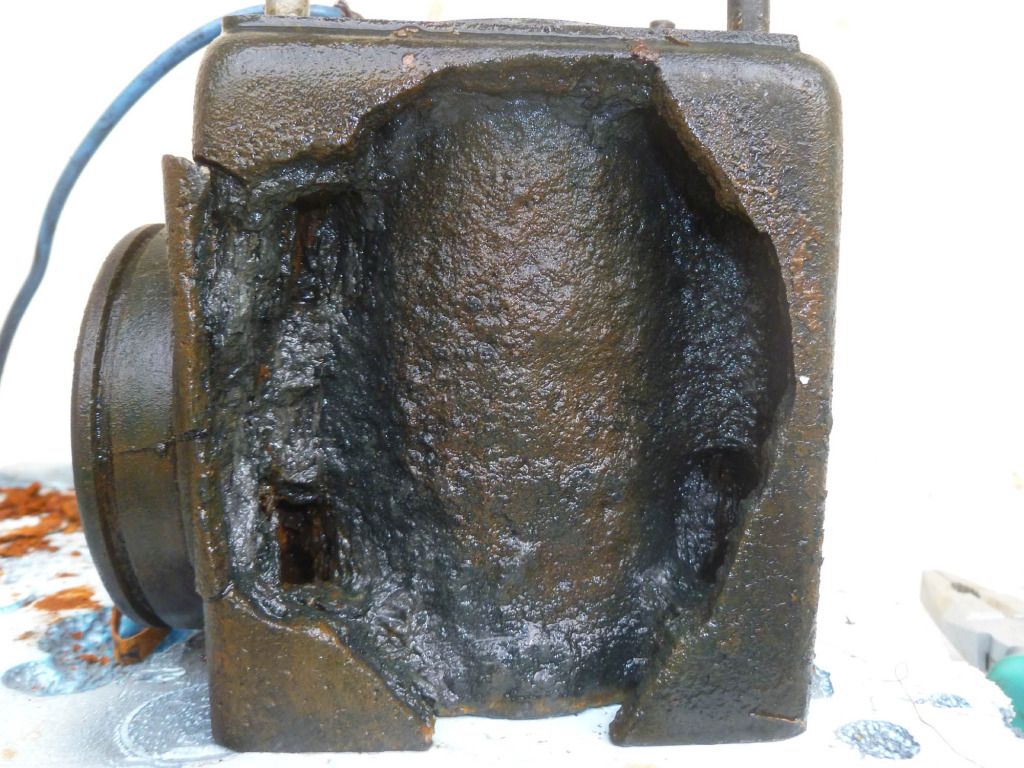
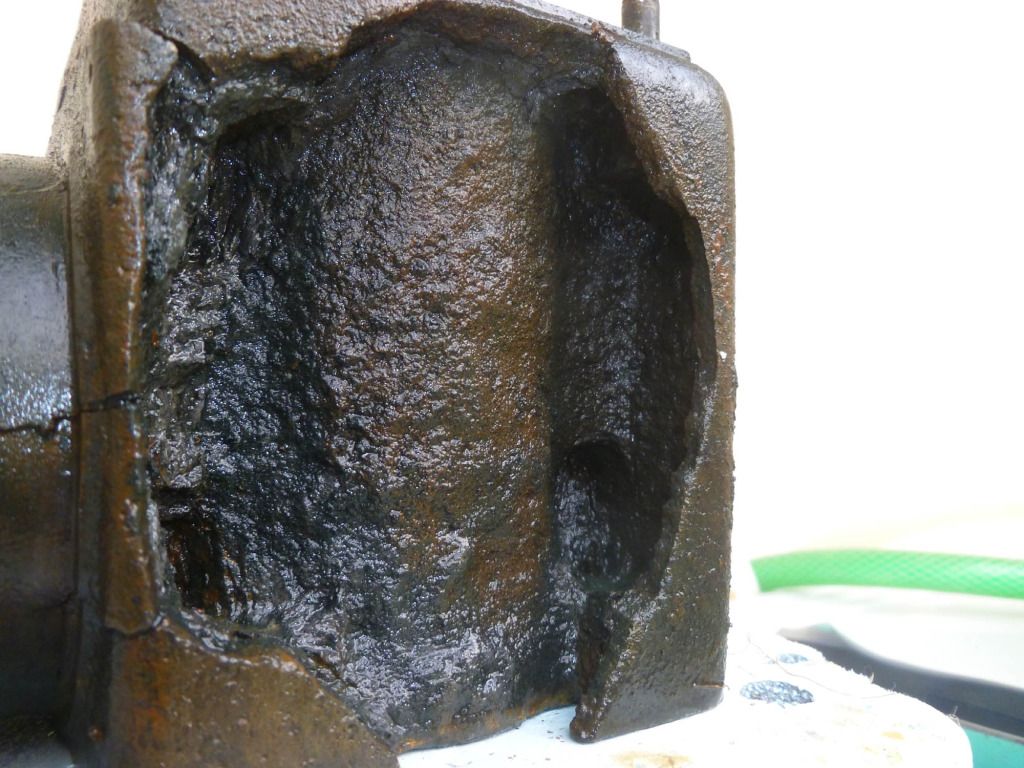
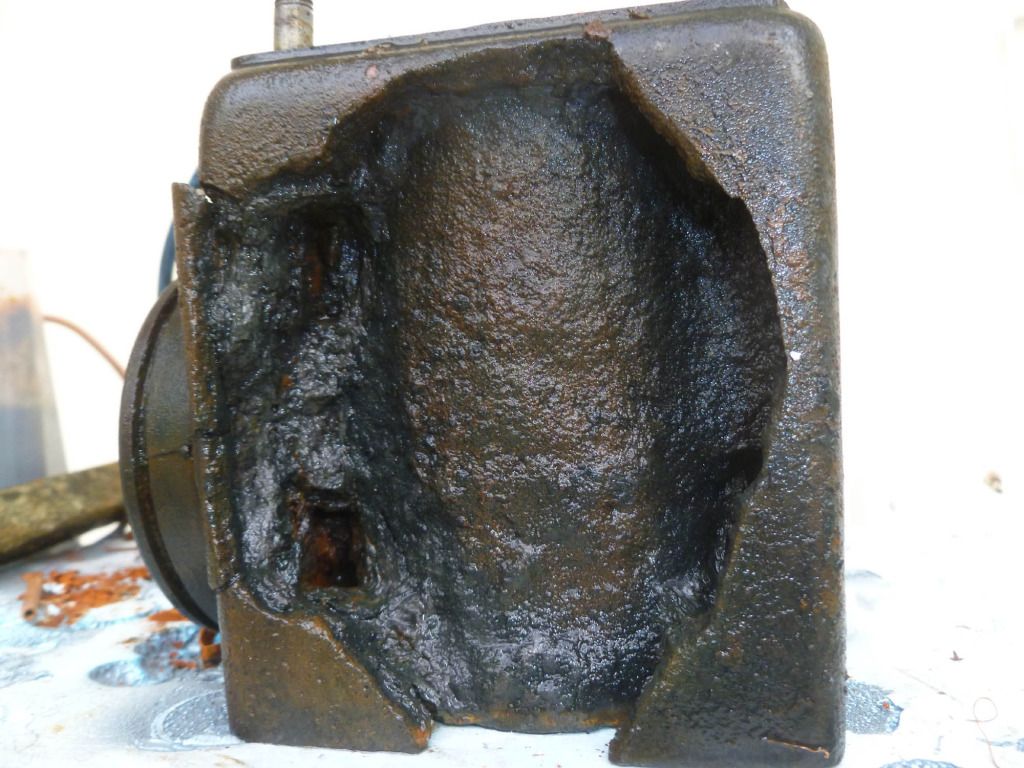
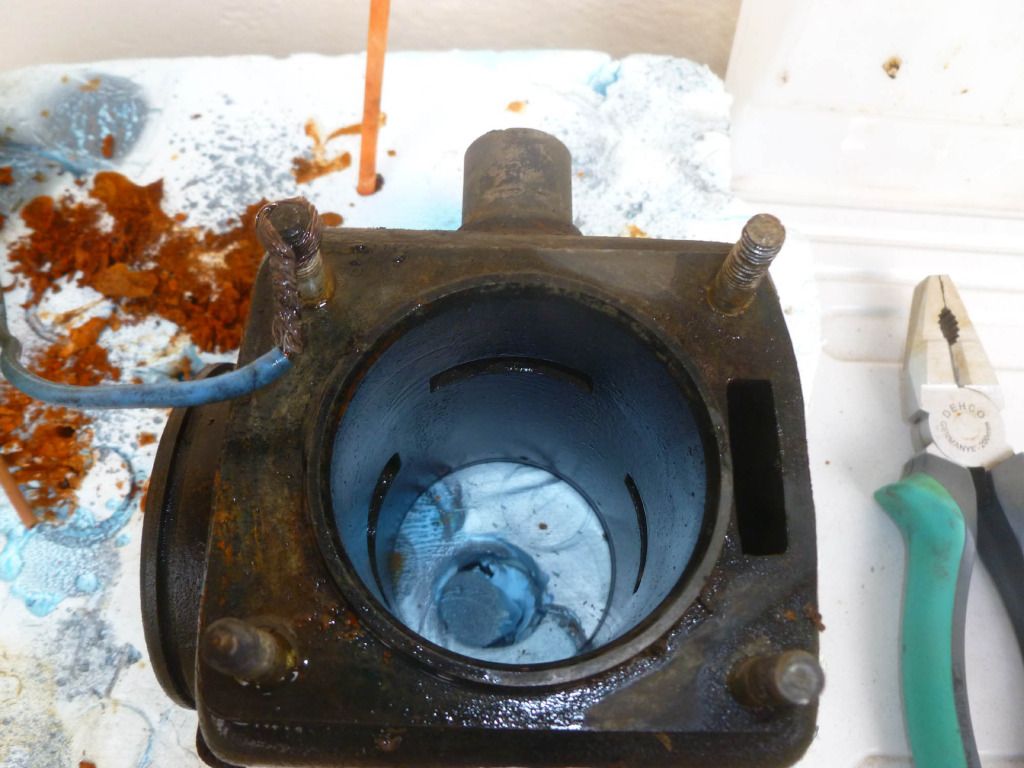
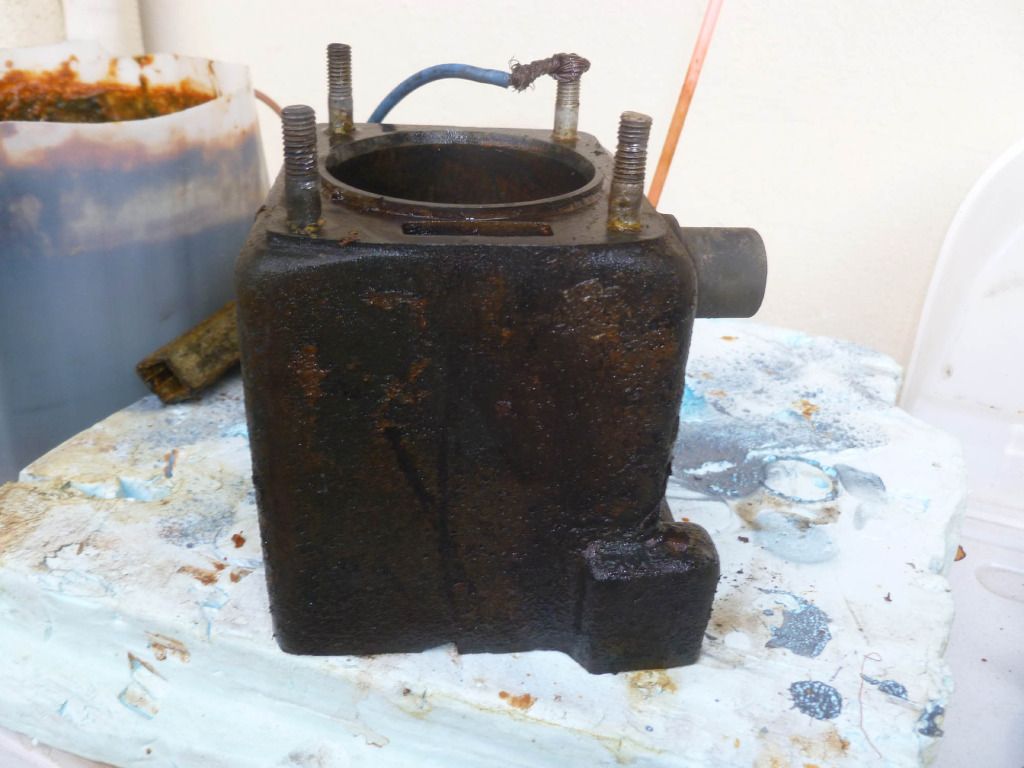
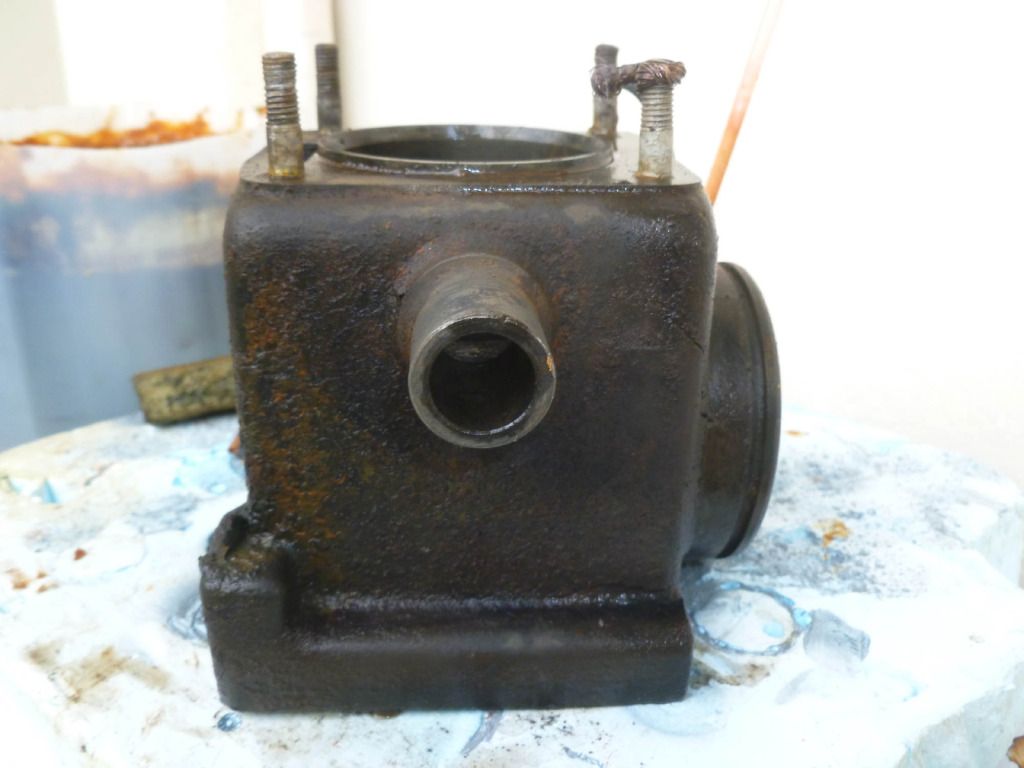

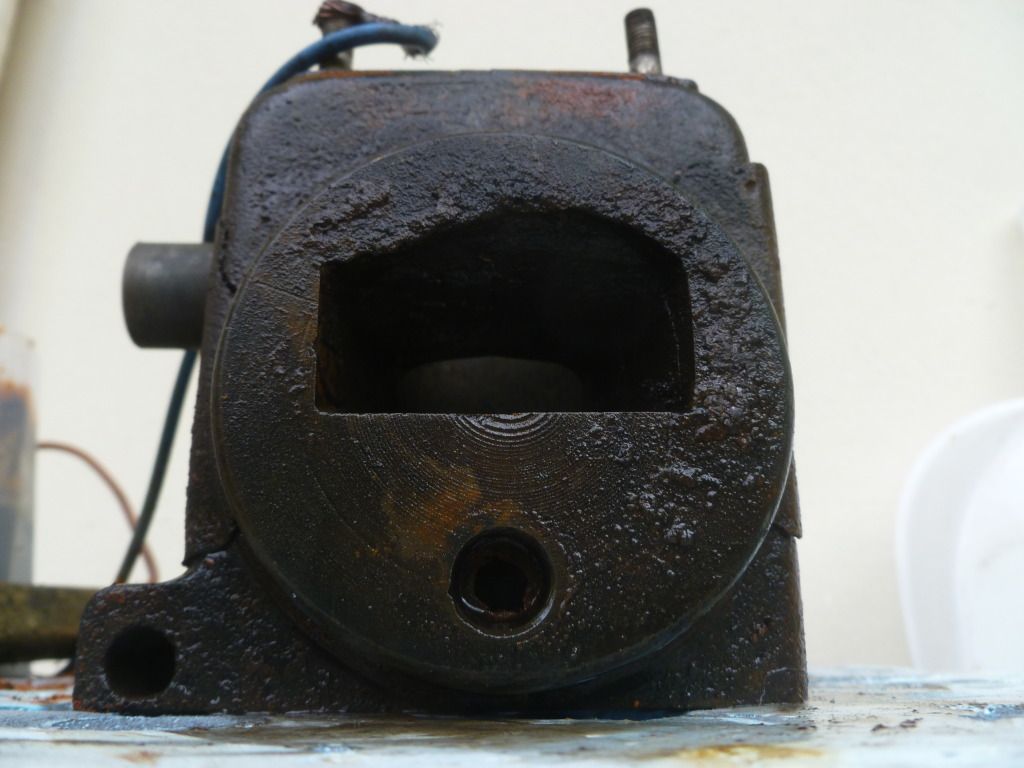
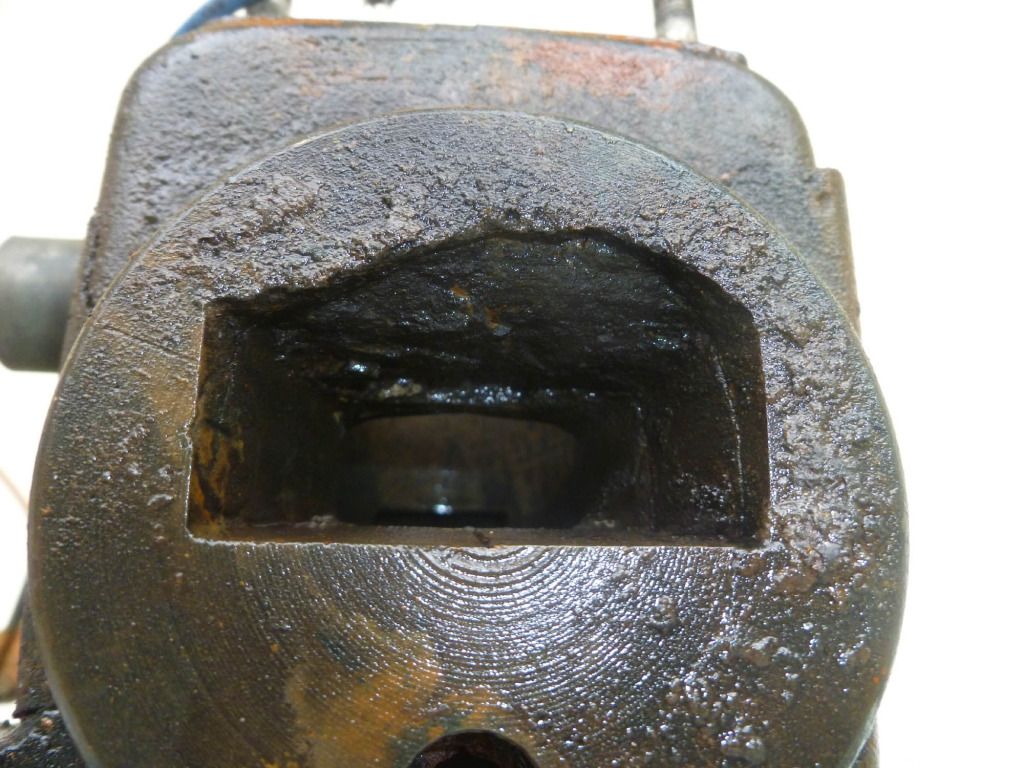
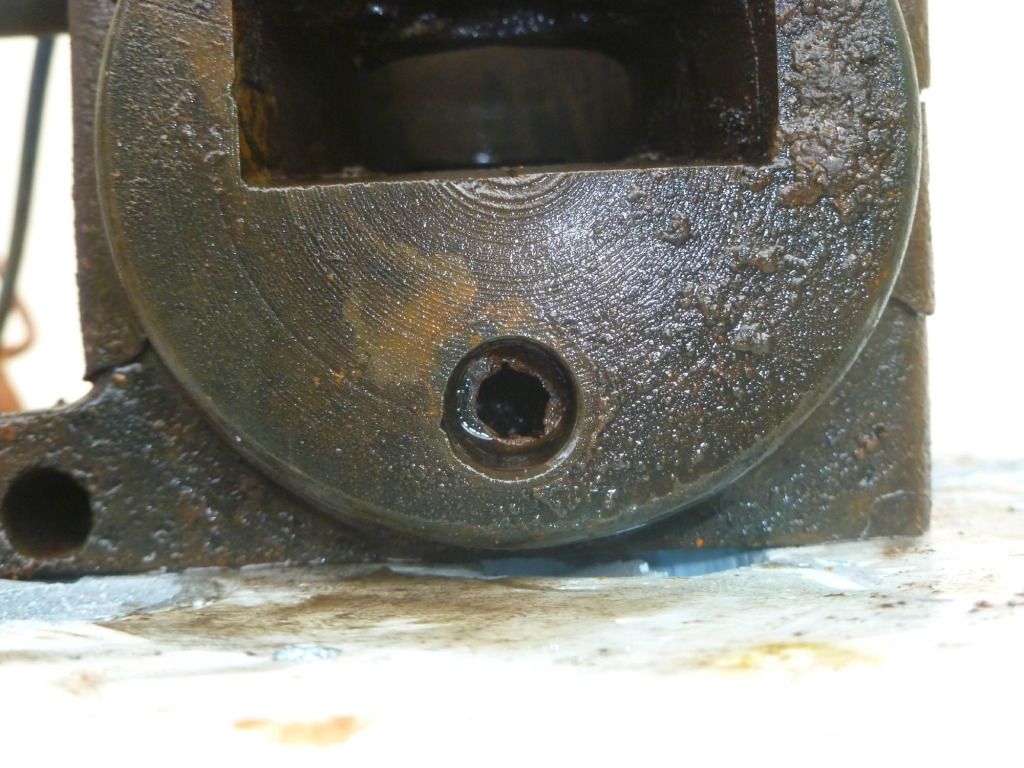
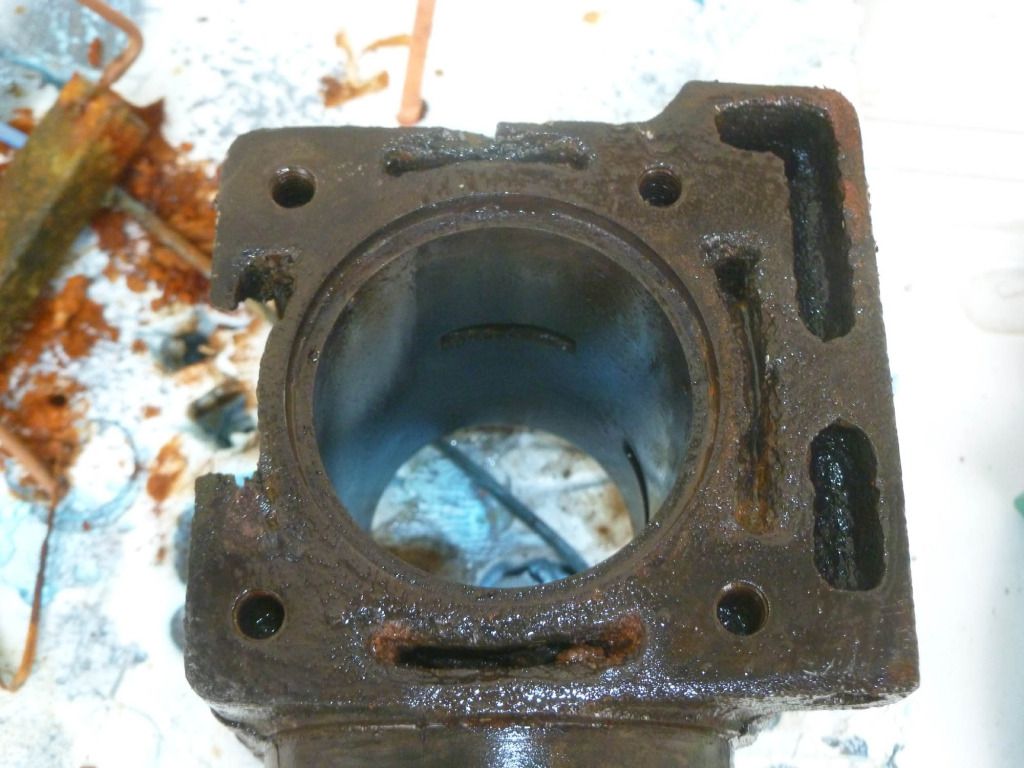
Seems to be working but it needs much more time than a couple of days. It certainly would be beneficial to use a round electrode which creates a cylinder and in the middle would be the block. High temperature increases the speed of the reaction, a lot of baking soda increases the temperature. I don't know exactly why, maybe because of making the solution more conductive.
Now staring at the pictures I think that this block must have left to soak well in salt water..!
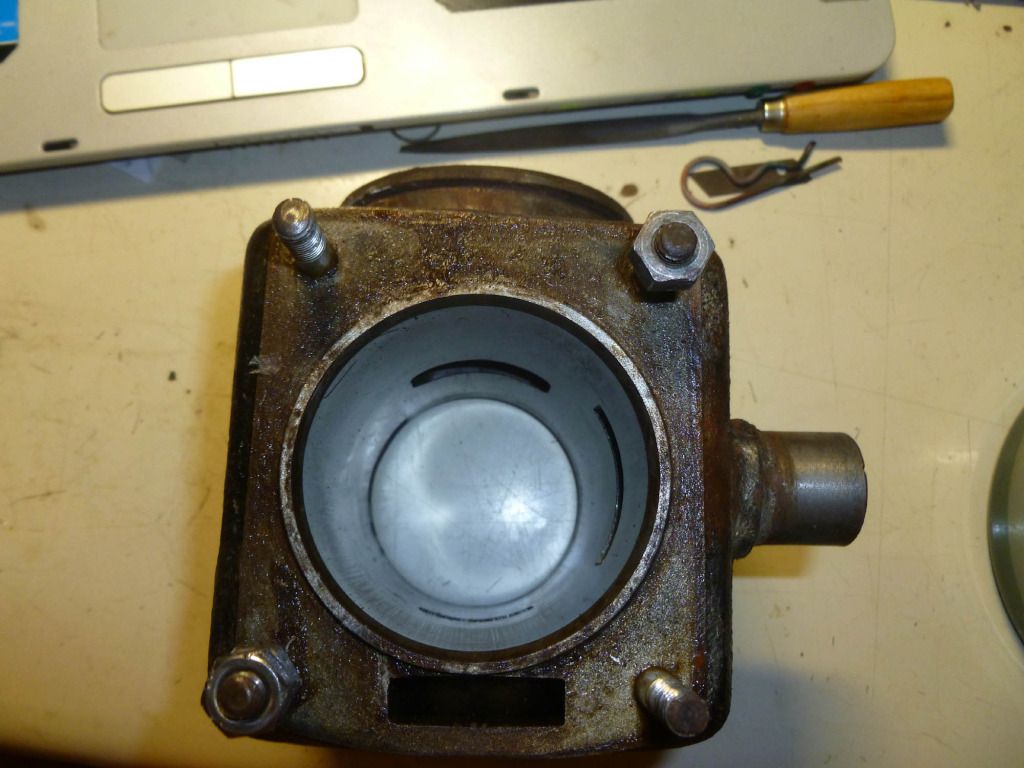
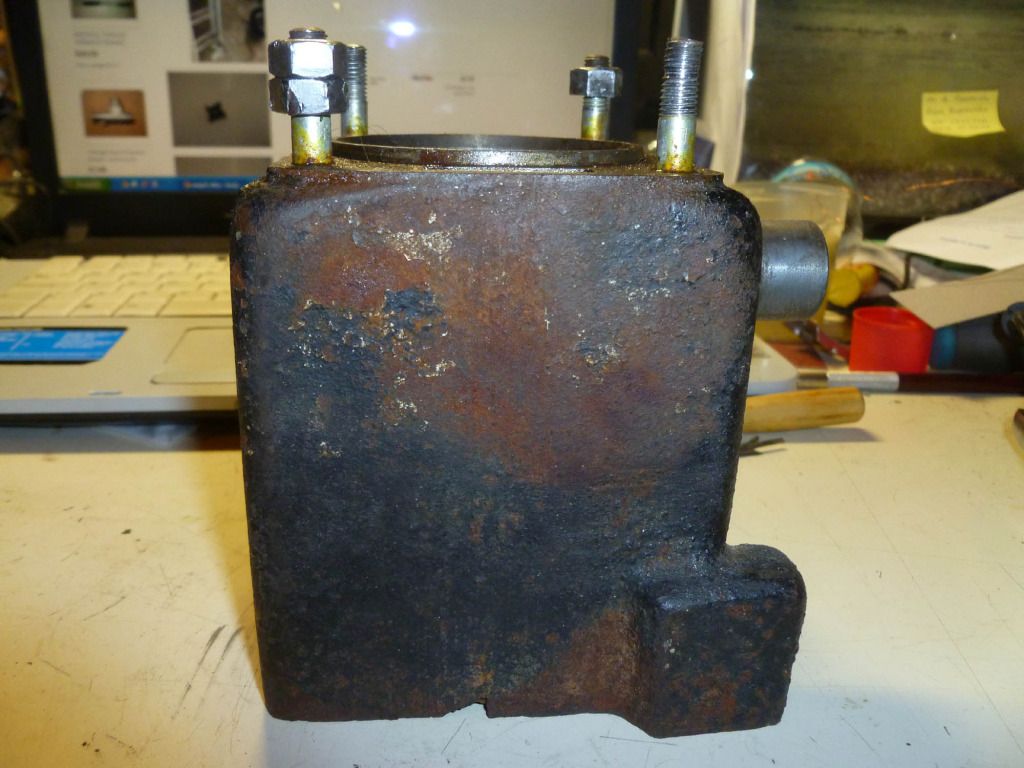
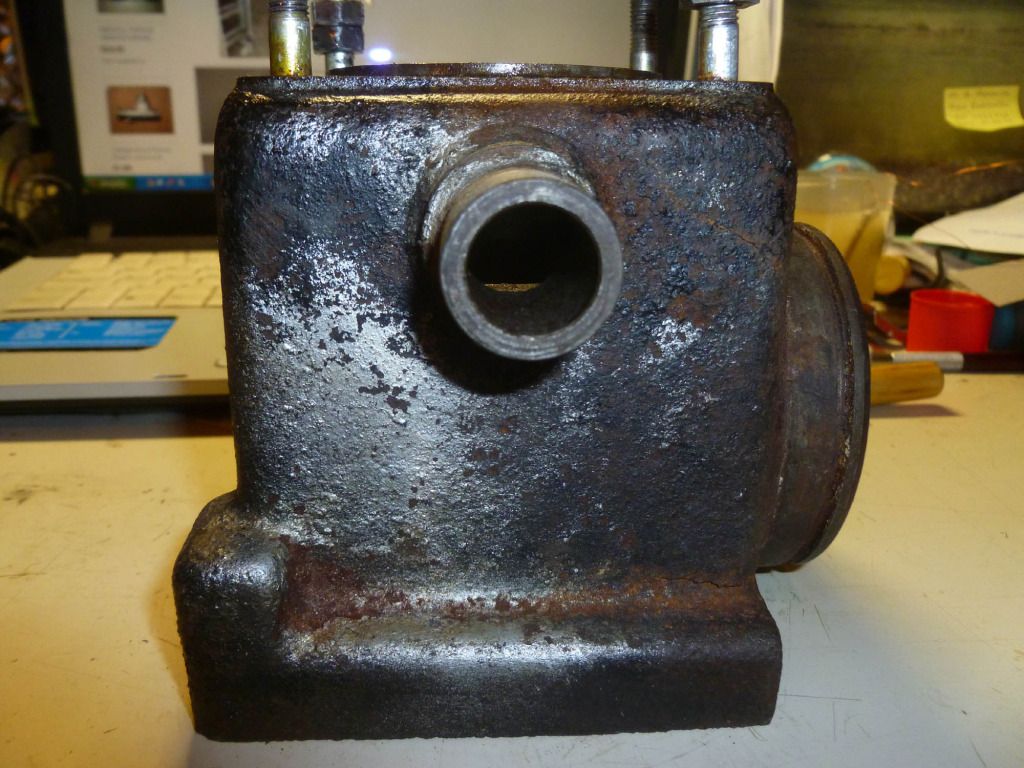
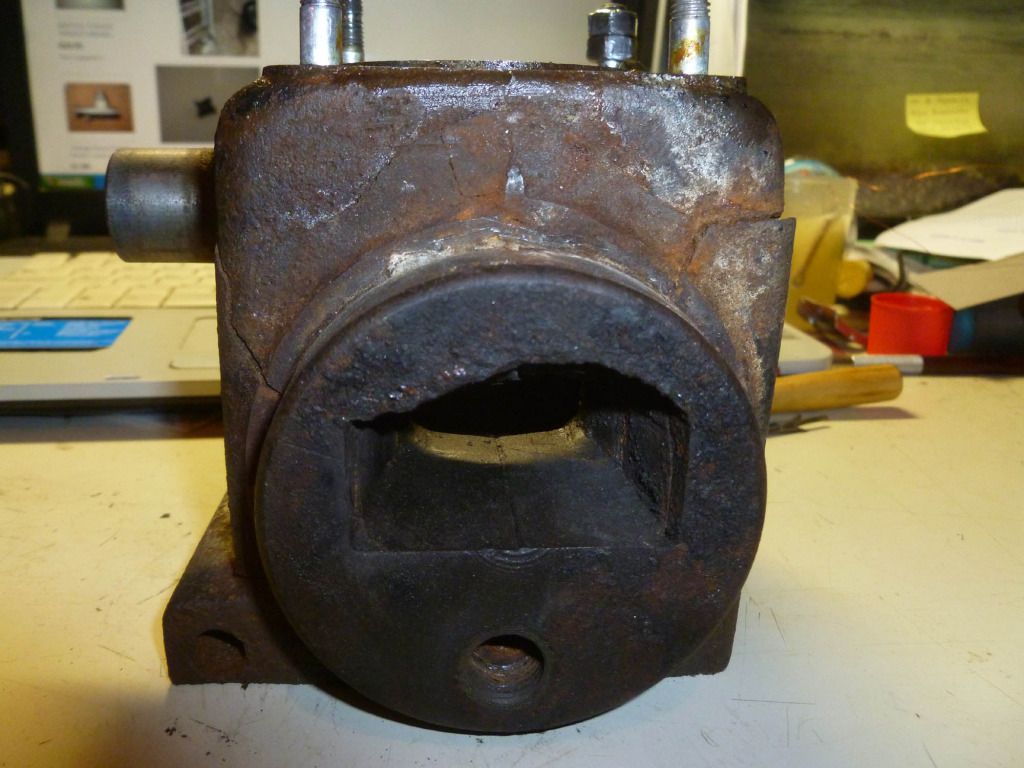
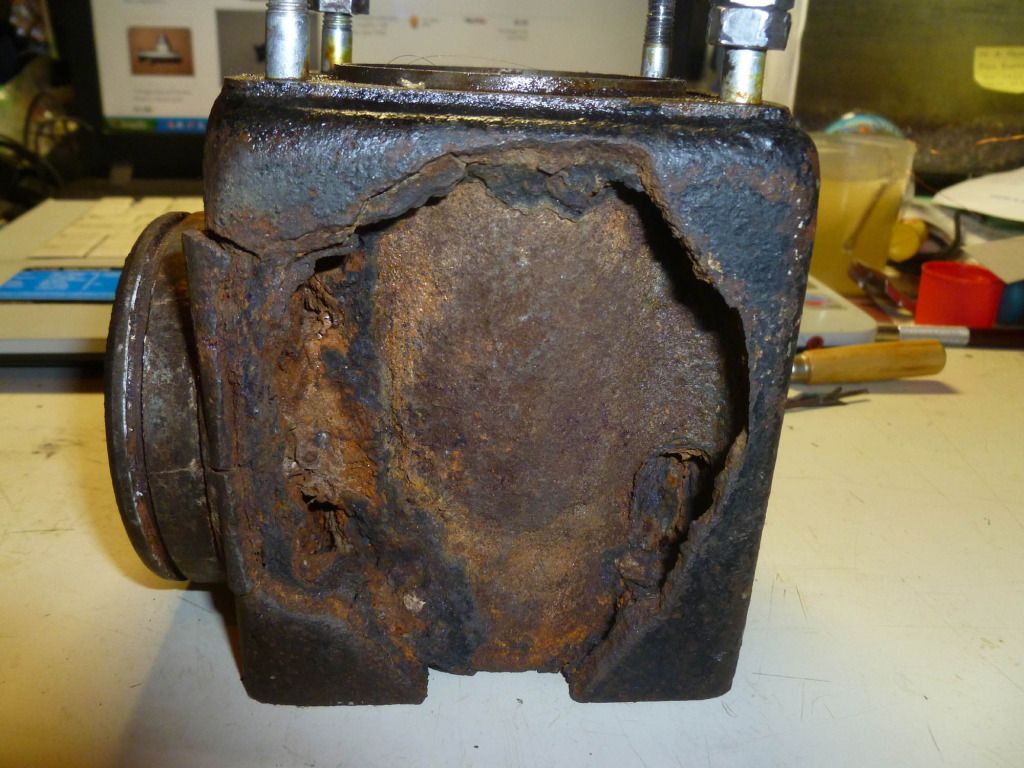
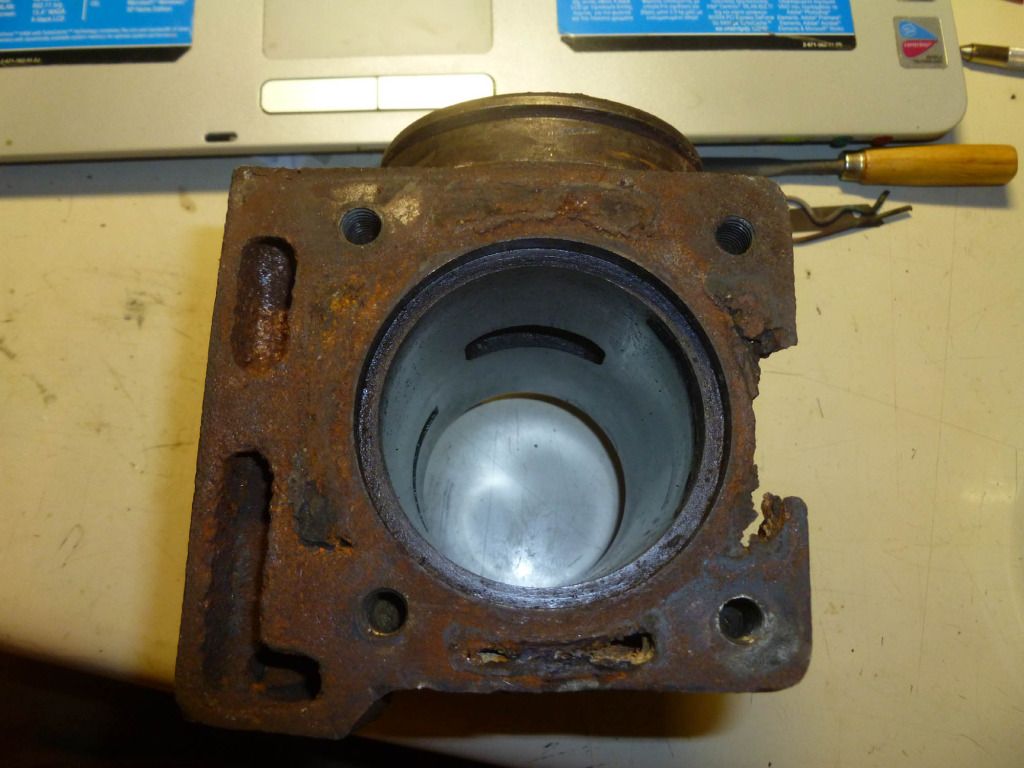
And this is after.
This is rust floating. I have changed the solution 3-4 times removing such amounts of rust but according to the visible results the procedure has to continue for many more days.
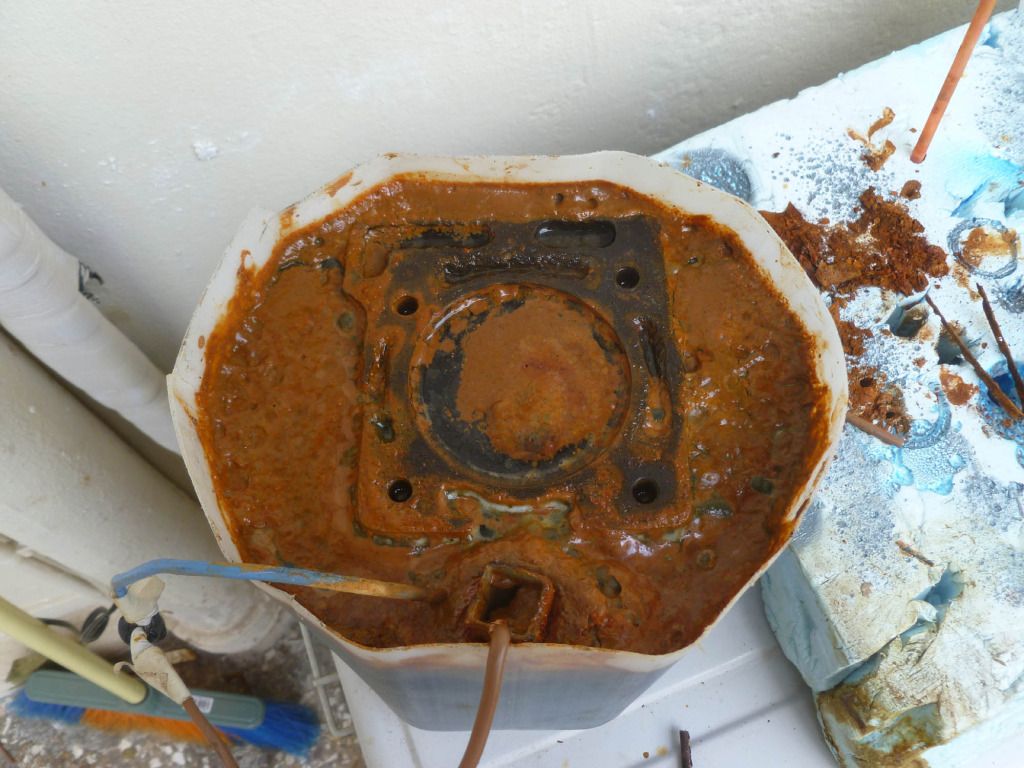
One sacrificial electrode.
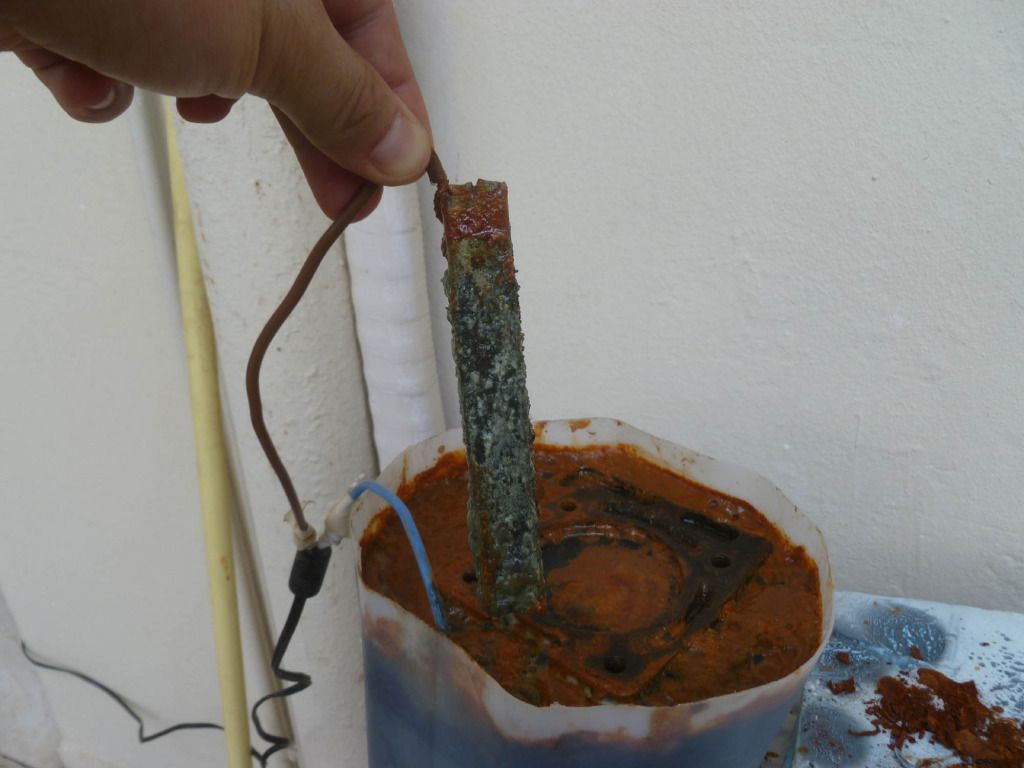
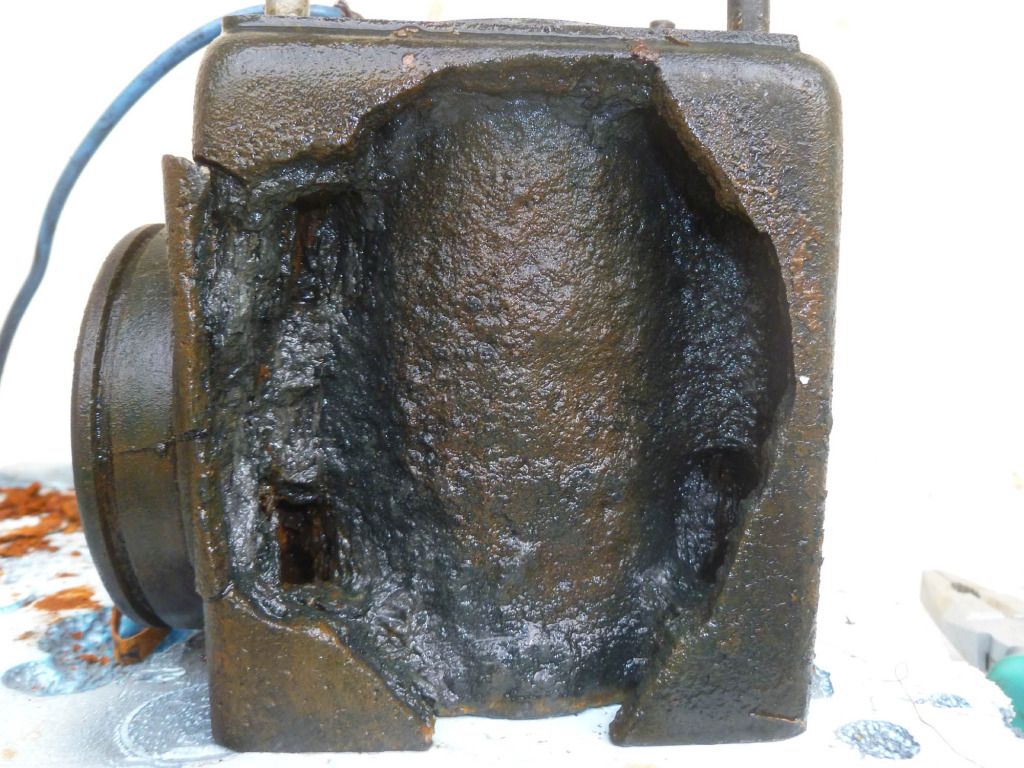
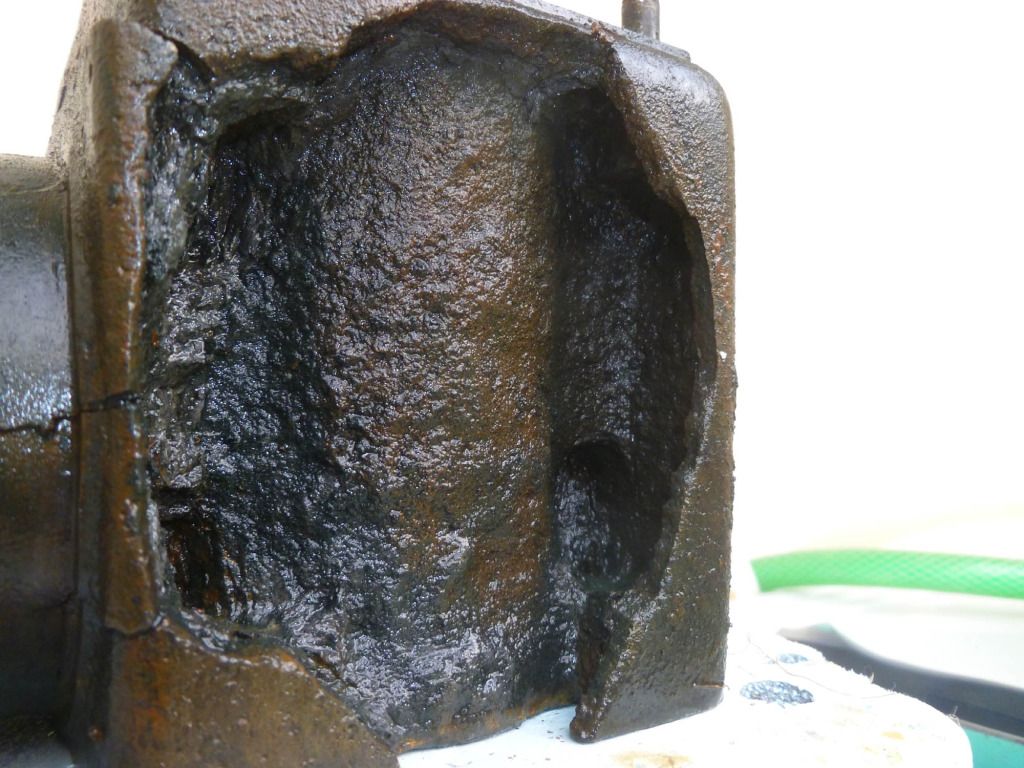
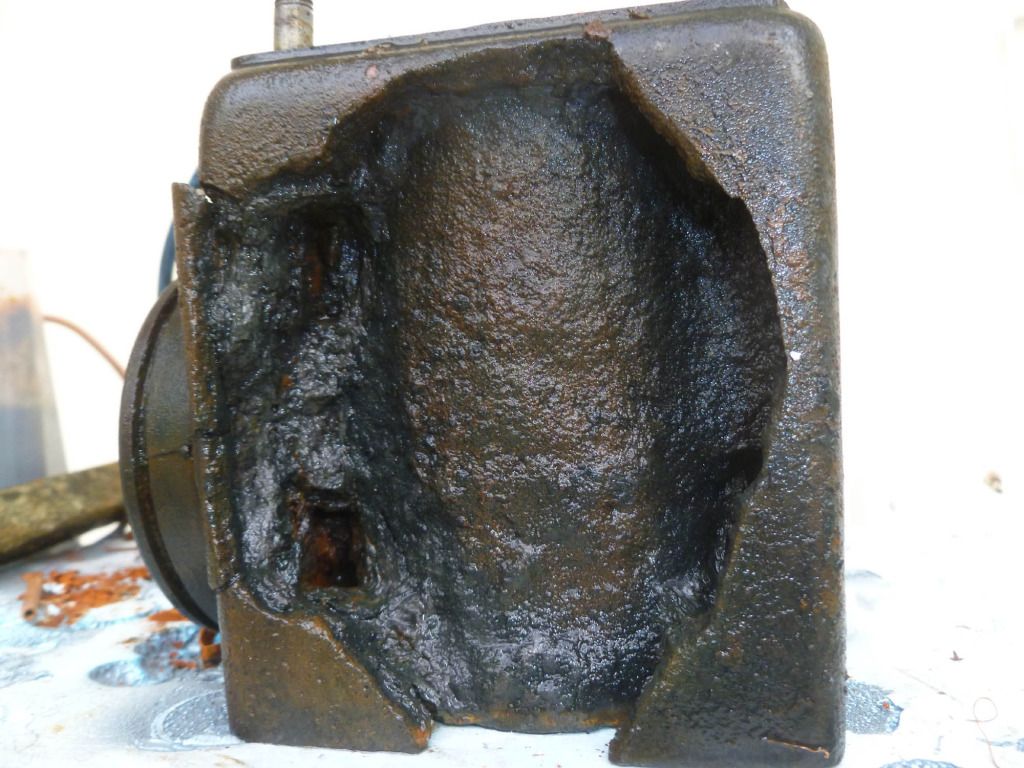
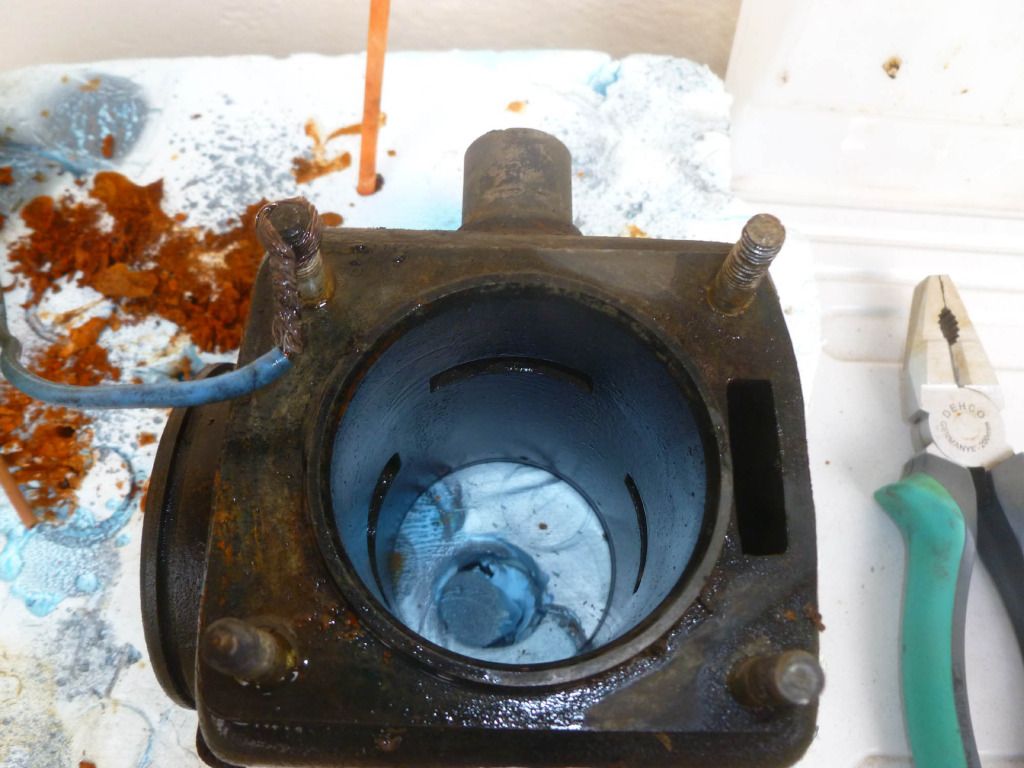
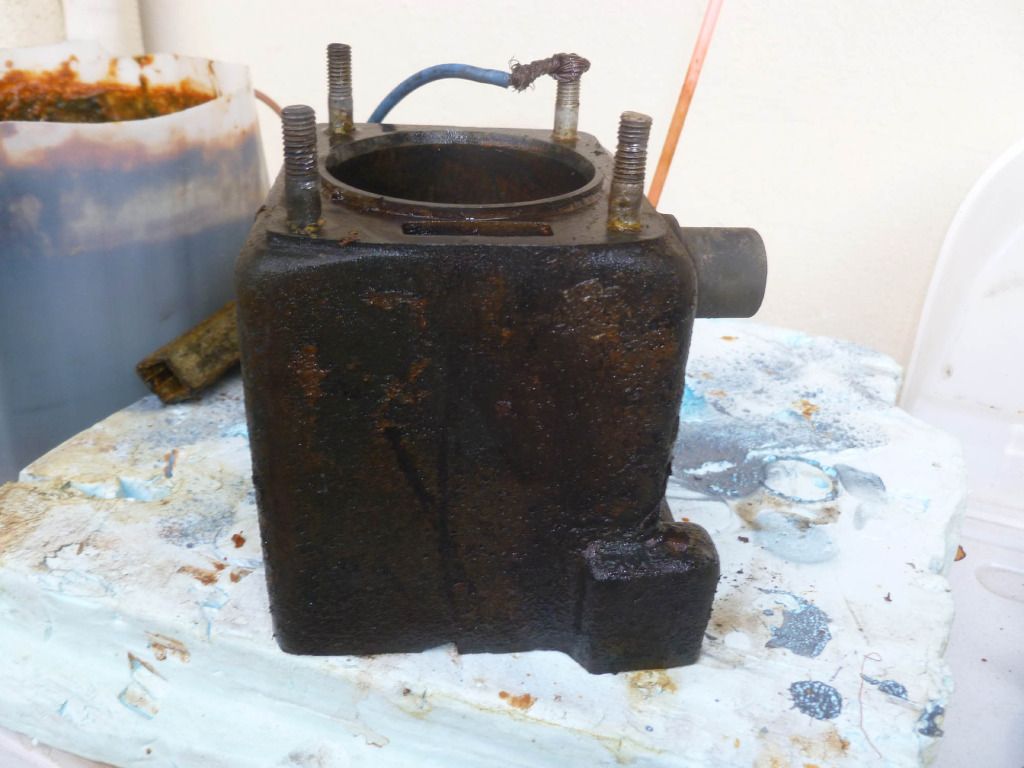
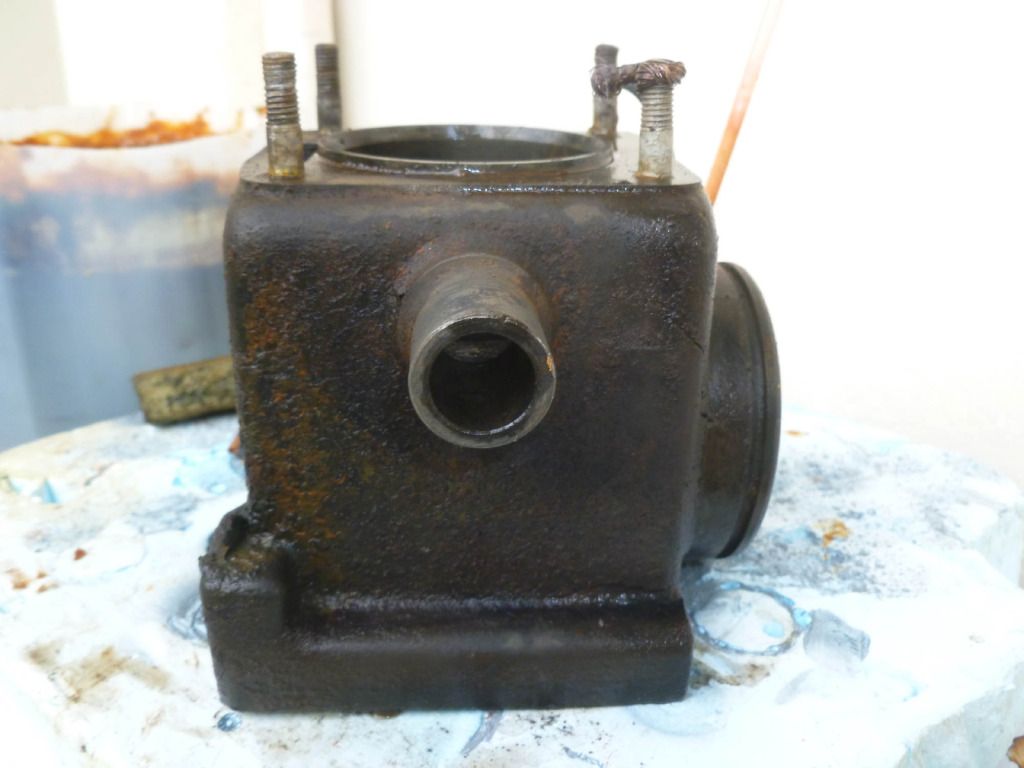

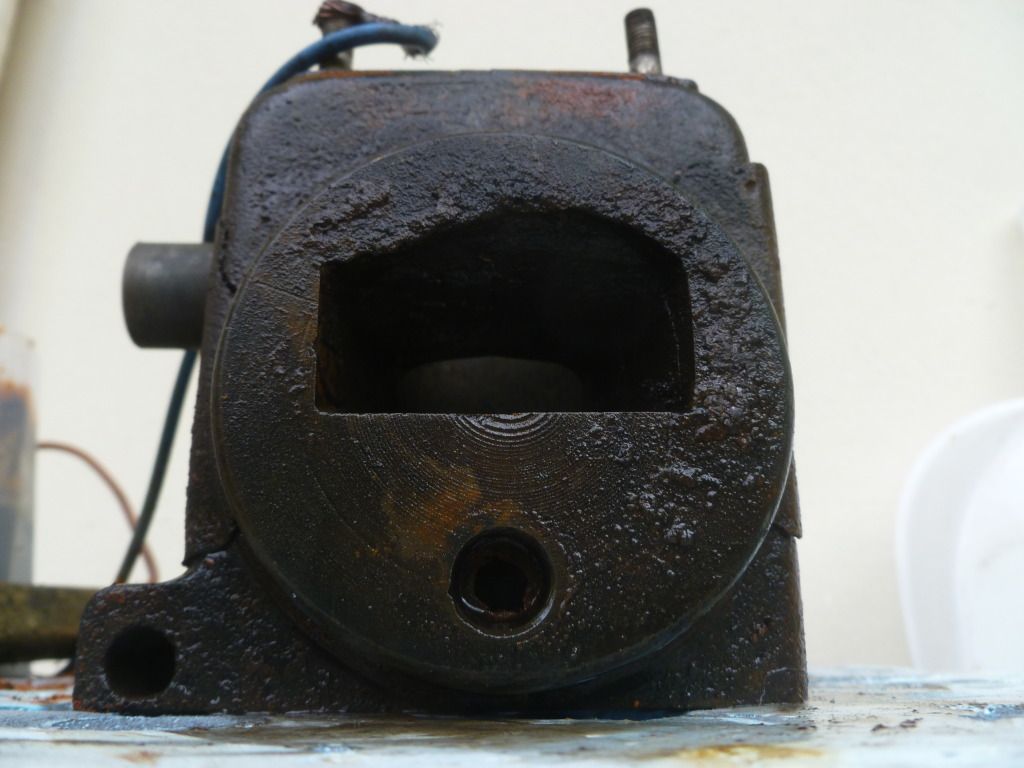
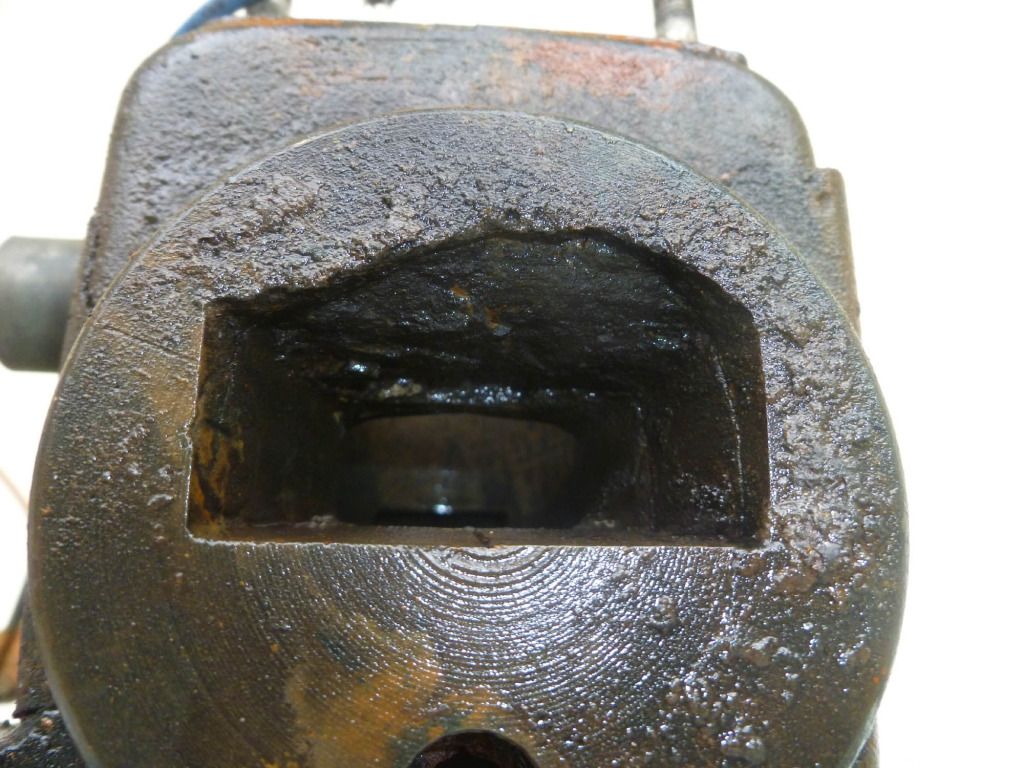
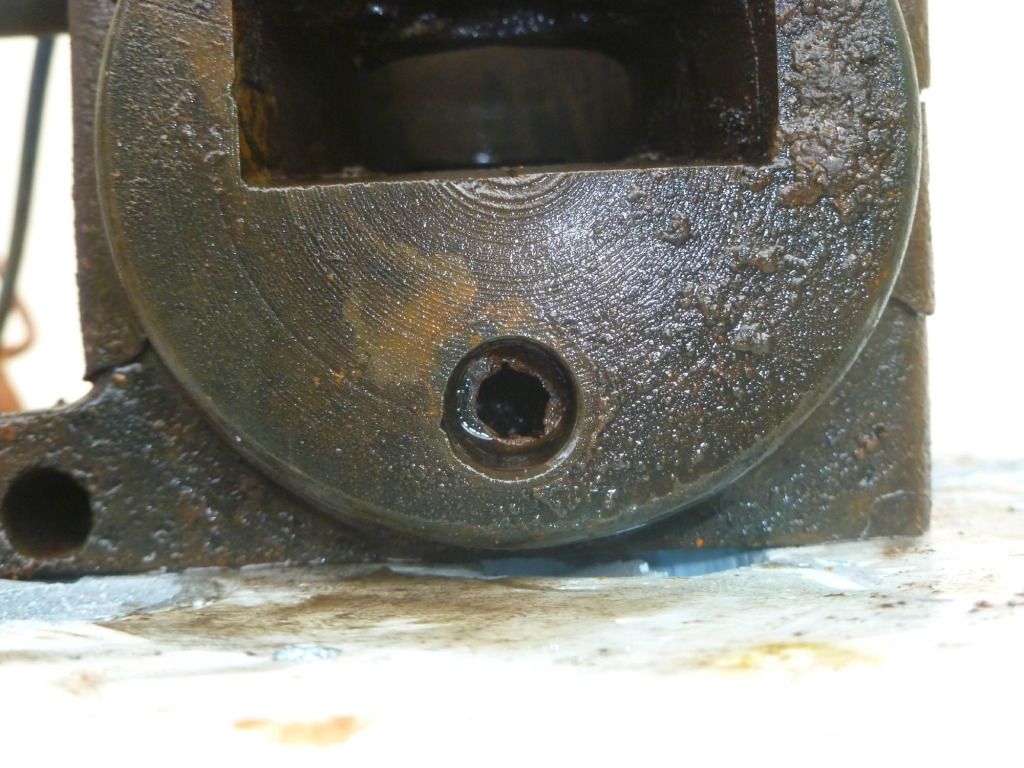
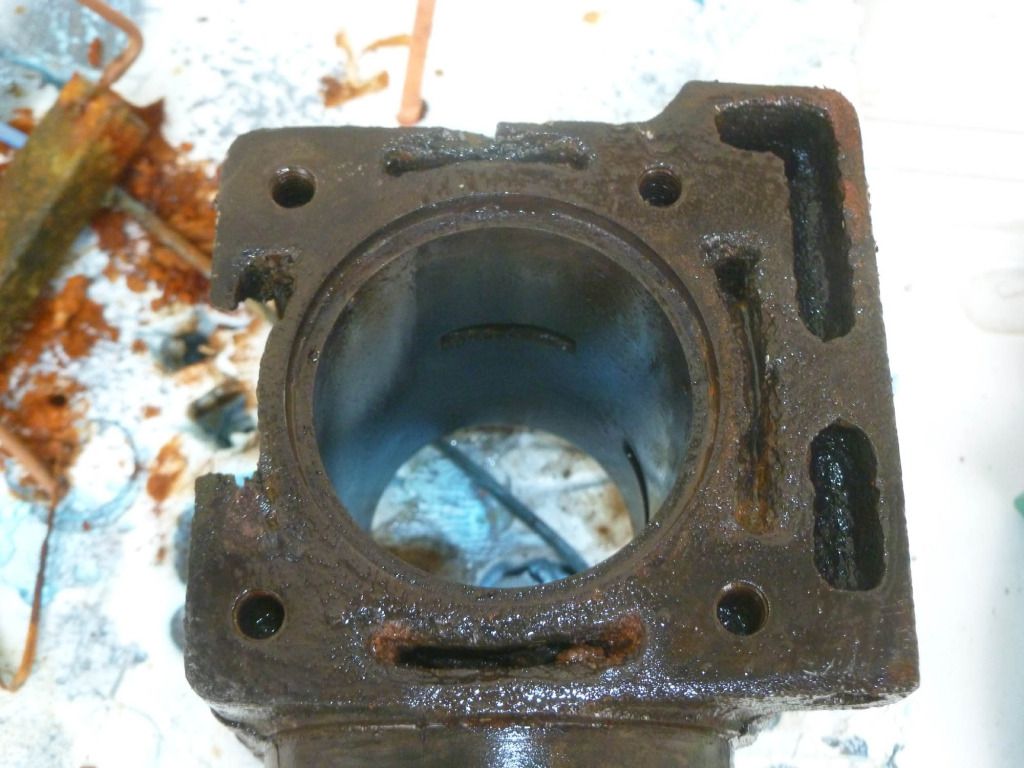
Seems to be working but it needs much more time than a couple of days. It certainly would be beneficial to use a round electrode which creates a cylinder and in the middle would be the block. High temperature increases the speed of the reaction, a lot of baking soda increases the temperature. I don't know exactly why, maybe because of making the solution more conductive.
Now staring at the pictures I think that this block must have left to soak well in salt water..!
I love the 10600/145 turns!!!
Re: Removing rust from water jacket
Molasses mix is between 7 to 1 and 10 to 1, my last mix was weaker as I added enough water to
cover the parts still worked.
John
cover the parts still worked.
John
- Collector Inspector
- Posts: 4196
- Joined: Sun Jun 29, 2008 4:32 am
- Location: Perth Western Australia
- Contact:
Re: Removing rust from water jacket
I have but one square block 102 and of course it is cracked.
Looks different to the ones in this topic. Why?
I will drill some holes and have a look later. Would it have the same little pockets as the sectioned photos show earlier?
Cheers
Looks different to the ones in this topic. Why?
I will drill some holes and have a look later. Would it have the same little pockets as the sectioned photos show earlier?
Cheers
A chicken is one egg's way of becoming others